these are the projects we are developing using natural Processes and absorbing effluents of a fossil fuel economy
All projects presented in the website are proprietary to Designs by Natural Processes, Inc.
The 6 Principles of designing with natural processes:
Self-Forming
Using Nearby/Waste Materials
Self-Repairing
Self-Sensing
Recycling
Improving the Environment
1. materials that SELF-FORM
A POLYMER CERAMIC COMPOSITE MODELED ON BONEs
(Left) A microscope photo of the cement/polymer material
(Right) The chemical delivery system for making this material in a mold.
2. Designing with nearby and/or Waste materials
Structural FLY ash Bricks and panels made from Coal fired FurnACEs
(Partner project with Magneco Metrel)
Use of ash from fossil fuel (coal) fired energy plants was made into panels at a company.
Ash from burning coal contains heavy metals and radioactive materials which can leach into the ground water if left as loose ash in potholes. Our process uses 99% ash to fabricate structural components so that the ash is sequestered and cannot leach out harmful chemicals.
Structures made from coal fired furnace ash
(Sponsored by Clean Coal Institute, Illinois)
Composition of raw ash (column 1) and leachate analysis results from fired ash showing sequestration of heavy and RCRA metals.
Sandwich panels were made from bottom ash and fly ash floaters/beads which give insulating properties to the panels.
Making Cement at Ambient Temperature Using 55% Municipal Solid Waste Ash - STTR Phase I & II
(Sponsored by DOE ARPA-E)
3. DESIGNING SELF-REPAIRING MATERIALS
Self-repairing concrete Projects
SELF-REPAIRING of cracks in full-scale CONCRETE Bridges
(Sponsored by National Science Foundation, Transportation Research Board, and National Academy)
(Left) Fibers being thrown into the cement mixer at the site
(Right) Fibers survive after being mixed into the bridge concrete.
The full scale bridges were made from commercially mixed concrete, into which the fibers filled with repair chemical were thrown. The fibers survived the mixing.
(Left) Fabrications of bridges and decks.
(Right) Released repair adhesive.
Full-scale, in-field concrete bridges were subjected to bending, in which internal shear cracking broke the fibers and released the repair adhesive. The bridges regained much of their strength due to this repair.
self-repairing concrete frames to represent buildings & Bridges
(Left) photo of frame containing internal self-repairing adhesives, cracking in the third static test, which shows cracking all over, but no catastrophic failure.
(Right) control without self-repair at same test
Hysteresis results of tests on self-repairing frames on the right, versus frames without repair chemical on the left
SELF-REPAIRING Polymer Composite Projects
Self-repairing airplane wings - SBIR phases I & II
(Sponsored by the US Air Force - WPAFB)
(Top Left) Layout of repair tubes on a graphite layer, simulating a self-repairing airplane wing.
(Top Right) A section cut through a self-repair graphite sample shows that upon impact, self-repair chemical went into numerous layers (darker grey lines) even though the repair tubes was in just one layer in the center.
(Bottom Left) Splayed graphite sample showing that the chemical is still liquid after processing at autoclave temperatures.
(Bottom Right) picture with black and yellow blobs.
Repair chemical survived process heating at 300-350 F heating for 2-3 hours. Chemicals fill all layers of damage in the laminate and repair takes 1-2 seconds.
self-repairing polymer composites for air vehicles
(Left) Compression after Impact (CAI) tests were done on graphite samples to assess the repair of the matrix resin. Three types of controls were made: non impacted samples no fibers, blue, impacted samples no fibers, red, impacted samples dummy repair chemical in fibers, blue. The repaired samples, yellow bar, restored 87% of non impacted controls, blue bar.
(Center) In-plane shear BM S4-23 was applied. In the chart, the repair sample, black bar, had a peak stress that is 82 % restoration of peak shear stress strength when compared to the non impacted control, white bar. It is a 36 % improvement over sample with tubes only, striped bar; that is the contribution of the repair chemical.
(Right) Test fixture used for testing in-plane shear of polymer composite specimens.
Self-repairing Polymer composite walls - SBIR Phases I & II
(Sponsored by the US ARMY ERCD CERL)
(Top Left and Right) Testing of many self-repairing composite panels showed survival of impacts as opposed to controls
(Bottom Left) Back-lit view of the forcefully impacted self-repairing panel.
(Bottom Right) Horizontal tubes with pink repair chemical show the chemical flowed out into a vertical crack. White areas in the tube have been voided of chemical.
Illumination of delaminations and self-repair chemical in forcefully impacted panels.
Testing of self-repairing composite panels survived impacts as opposed to controls.
(Left) Self-repair panel with 5 impacts approximate to each other
(Right) Fiberglass panel cut to show cross section of self-repaired impact areas. Long lens shapes are the self-repaired delaminations.
Self-repairing panels survived multiple approximate impacts as opposed to controls.
Self-repairing Polymer composite walls - a rapid innovation fund (rif) project
(Sponsored by the US Army ERDC)
(Left) Field blasted panels with sensors behind.
(Center) Arena set-up panels
(Right) A self-repairing panel shows the results of impact by the concentric circles of the moire pattern
Tests on Thrice Tested Panels Showed Self Repairing Panels Stopped Impact Particles But Controls Did Not
(Left) making self repairing panels using the hot press process.
(Right) The self repair system inserted into the pultrusion process.
Self-Repairing wall panels were successfully processed with two companies using two different processes.
(Left) commercially processed wall panel at Armortex using wet resin infusion and a press into which self-repairing fibers were inserted.
(Center) the repair tubes are on a layer of vinyl ester panel.
(Right) self-repairing vinyl ester armor panels made at Armortex.
self-repairing composite Pipelines
(Top Left) Typical un-impacted test sample.
(Top Right) An impact pipe to cut to obtain test specimens.
(Middle Left) Tensile test fixture with sample ready to test.
(Middle Right) Tested and broken self-repair roving sample.
(Bottom) Set of pipe samples.
Self-repairing polymer pipes successfully resisted burst pressure.
Self-repairing composite walls for pressurized habitats or vehicles
(Performed at the request of NASA)
From left to right: (1) Experiment for testing in space. (2) Damage caused by a small object impact in space. (3) The regenerative composite wall sample is placed over a vacuum pot and then punctured with a 0.075" metal punch tip that made a 0.155" diameter hole. (4) The vacuum gauge showed that the pressure of 27 inches of mercury were maintained after the puncture and subsequent removal of the metal punch. (5) The sample was taken off the vacuum pot and there was no evidence of colored repair material being pulled from the sample into the vacuum pot.
self-repairing elastomeric materials (rubber Tires)
(Left) Self-repairing material on the inside of a truck tire.
(Right) Puncturing a truck tire with a nail on a stick.
The truck tire maintained its pressure for 50 days.
Self-repairing of truck tires was successful over the long term.
4. Designing materials that self-sense
Self-sensing composites
(Top Left) Forcefully impacted composite panels.
(Top Right) Splayed forcefully impacted composite panels show the reacted repair chemical, which turns yellow in reaction.
(Middle and Bottom Rows) Low and medium frequency eddy current scans could detect one type of metal coated tubes.
self-sensing concrete
(Top Left) Laser light was passed through the tubes to evaluate how much chemical remained inside the tube. This was an indirect way of measuring the volume of the cracks.
(Top Right) Graphs show a linear correlation between the laser light diffraction pattern and the quantity of liquid voided from the capillary pipettes.
(Bottom) By comparing the amount of light scattered back at different times, the optical time domain reflectometry (OTDR) can determine losses. OTDR transmits an optical pulse through an optical fiber and measures the fraction of light that is reflected back.
5. MATERIALS THAT RECYCLE THEMSELVES
PRESTRESsED CONCRETE BRIDGE GIRDERS THAT ARE SAFELY DEMOLISHED
(Performed with Egyptian Concrete Co.)
(Left) A bed for making prestressed concrete girders has steel tendons with self-repairing tubes around them.
(Right) Pouring concrete over the self-repairing tubes.
Prestressed concrete contains girders under high stress that compress the concrete in order to improve tensile strength. This allows for stronger, more durable concrete parts. During demolition, however, the immense energy stored in the girders can be suddenly released, leading to property damage and unsafe conditions.
Designs by Natural Processes has developed an effective method for safely dismantling these building elements by releasing the stored energy in smaller, easily controlled energy increments.
6. MATERIALS THAT IMPROVE THE Environment FOR OTHERS
A COATING FOR CONCRETE THAT ABSORBS CO2, GIVES OFF OXYGEN WHILE STRENGTHENING THE CONCRETE
(Funded by the National Science Foundation)
The graph shows as our coating absorbs carbon dioxide, it releases oxygen over time.
- Surface coated with XSi5O11
- Surface patched with C-S-H and sand mixture
- Surface coated with XSi5O11 and then with C-S-H and sand mixture
- Surface that had no application
Depth of carbonation in coated bridges (lighter area) was greatest in areas with our coating (#1), versus the control (#4).
A DESIGN THAT uses all 6 principles
AN OCEAN PORT/CITY design using the chemistry of seawater
Designs by Natural Processes is drawing from the “experience” of evolution. To make an ocean port relies on using the same chemicals which undergo different forces from nature and use various natural processes such as those which occur in coral. It integrates many separate functions using the human body as an analogy such as self formation (bone), sensing (nerves), repair (piezoelectricity), self recycling and improving the environment (takes up carbon dioxide).
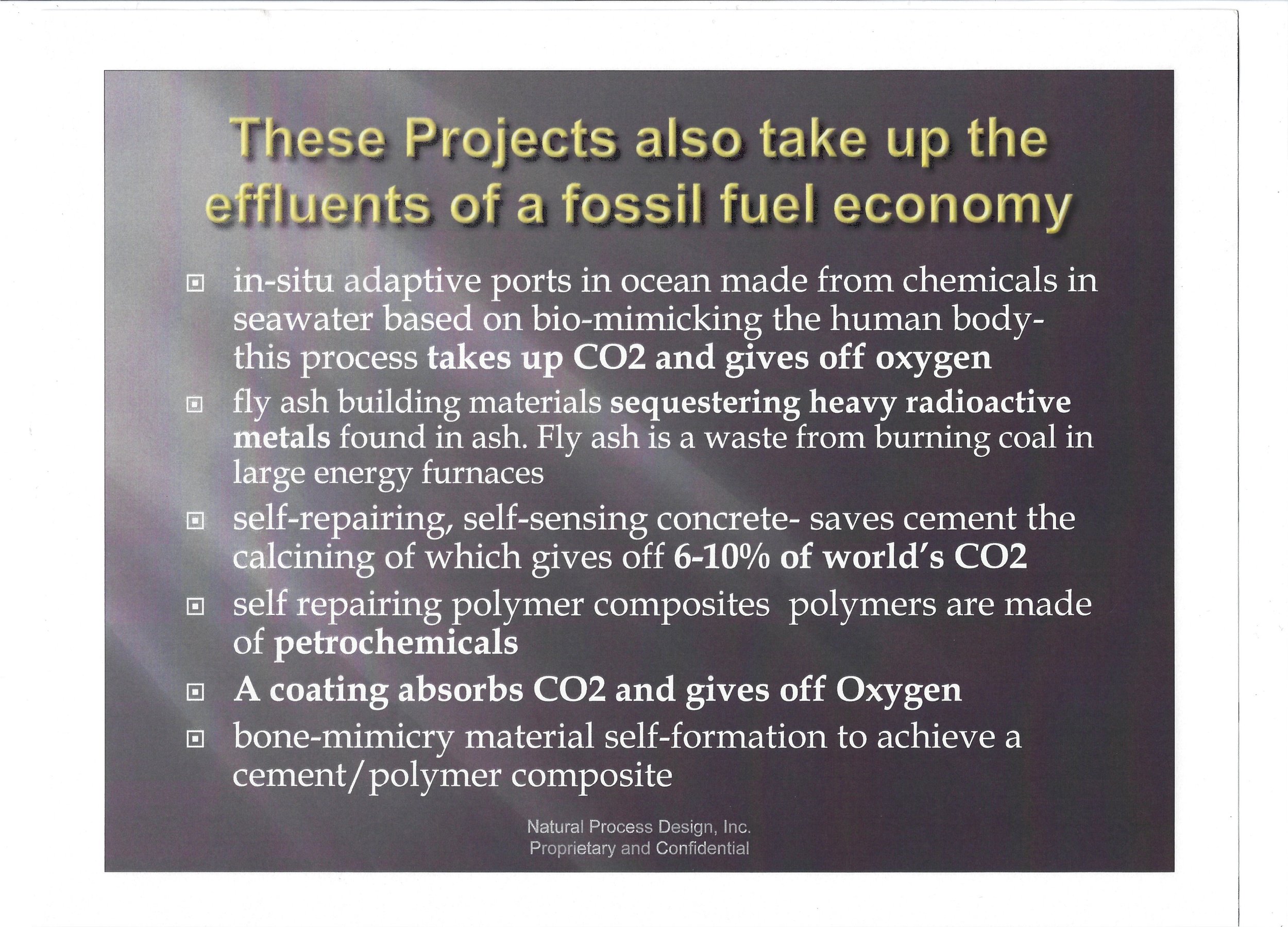
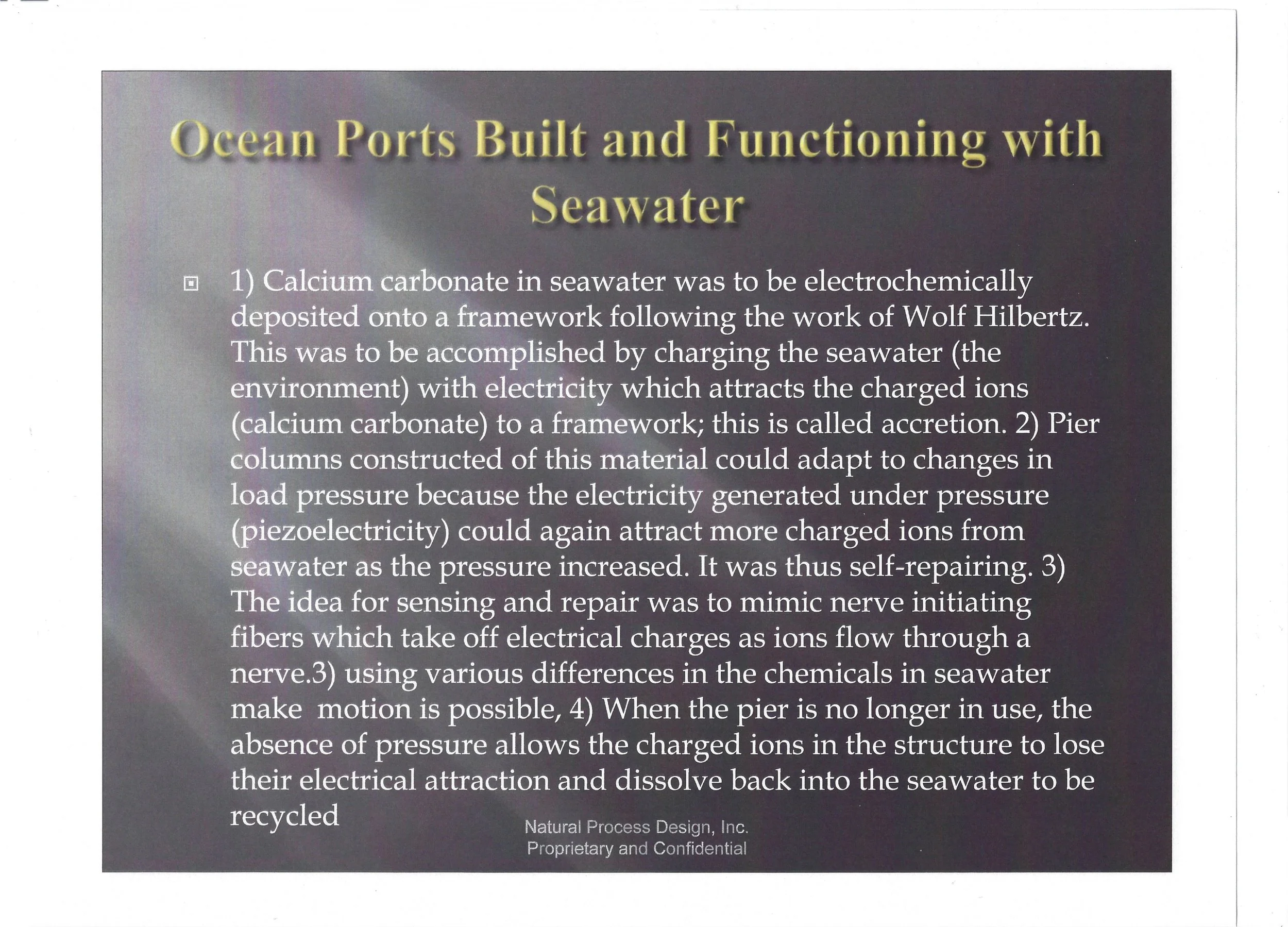
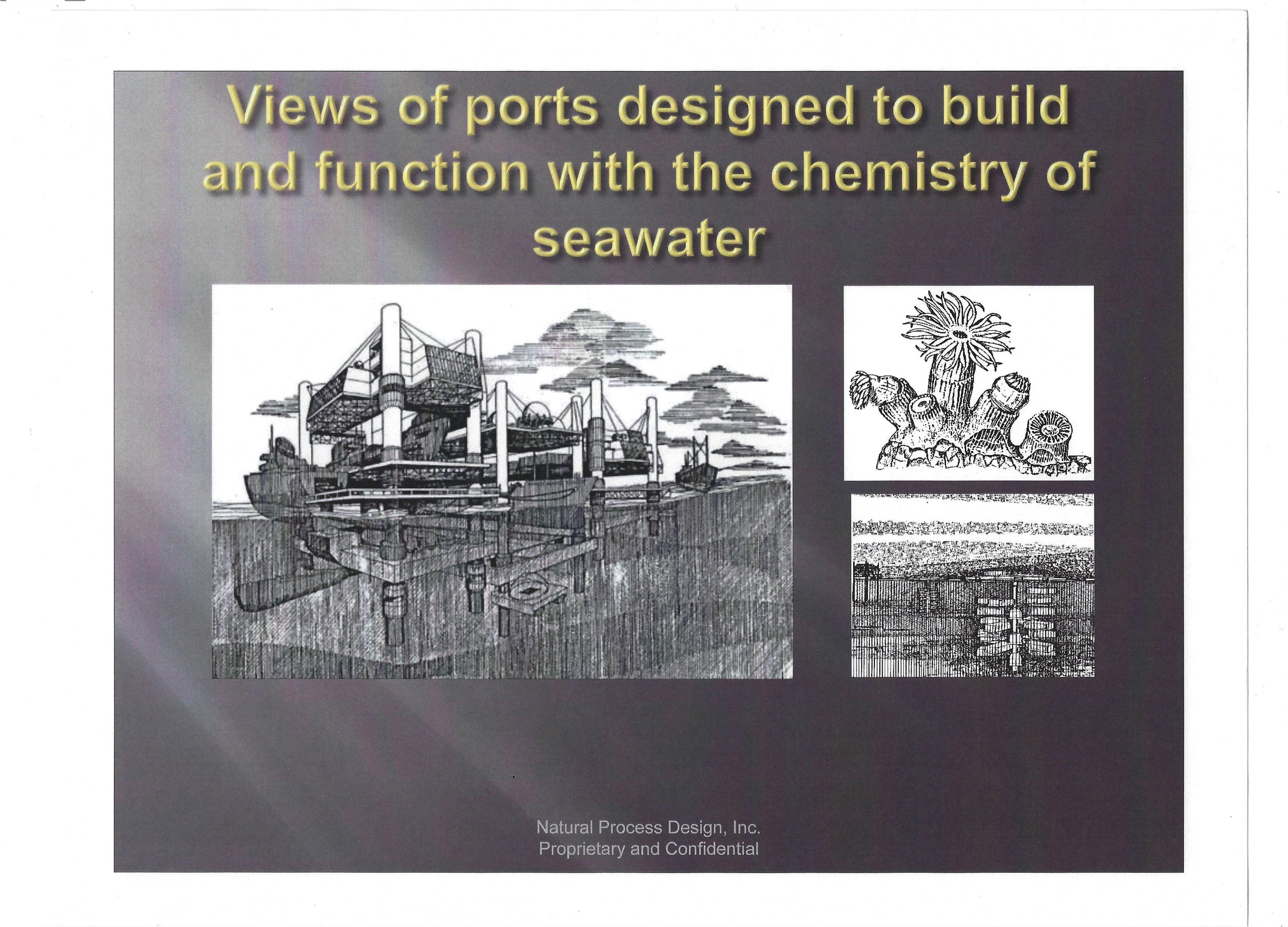
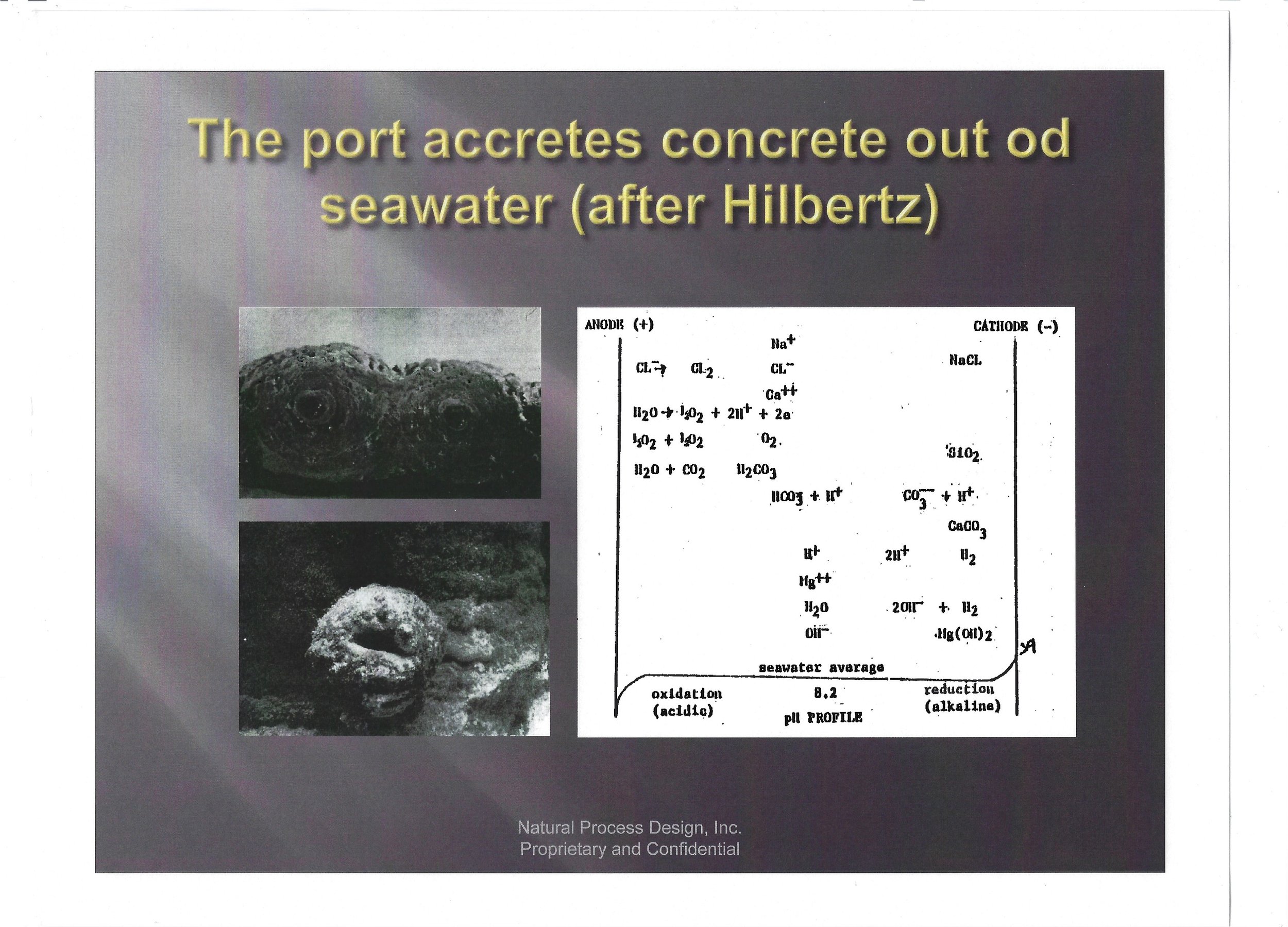
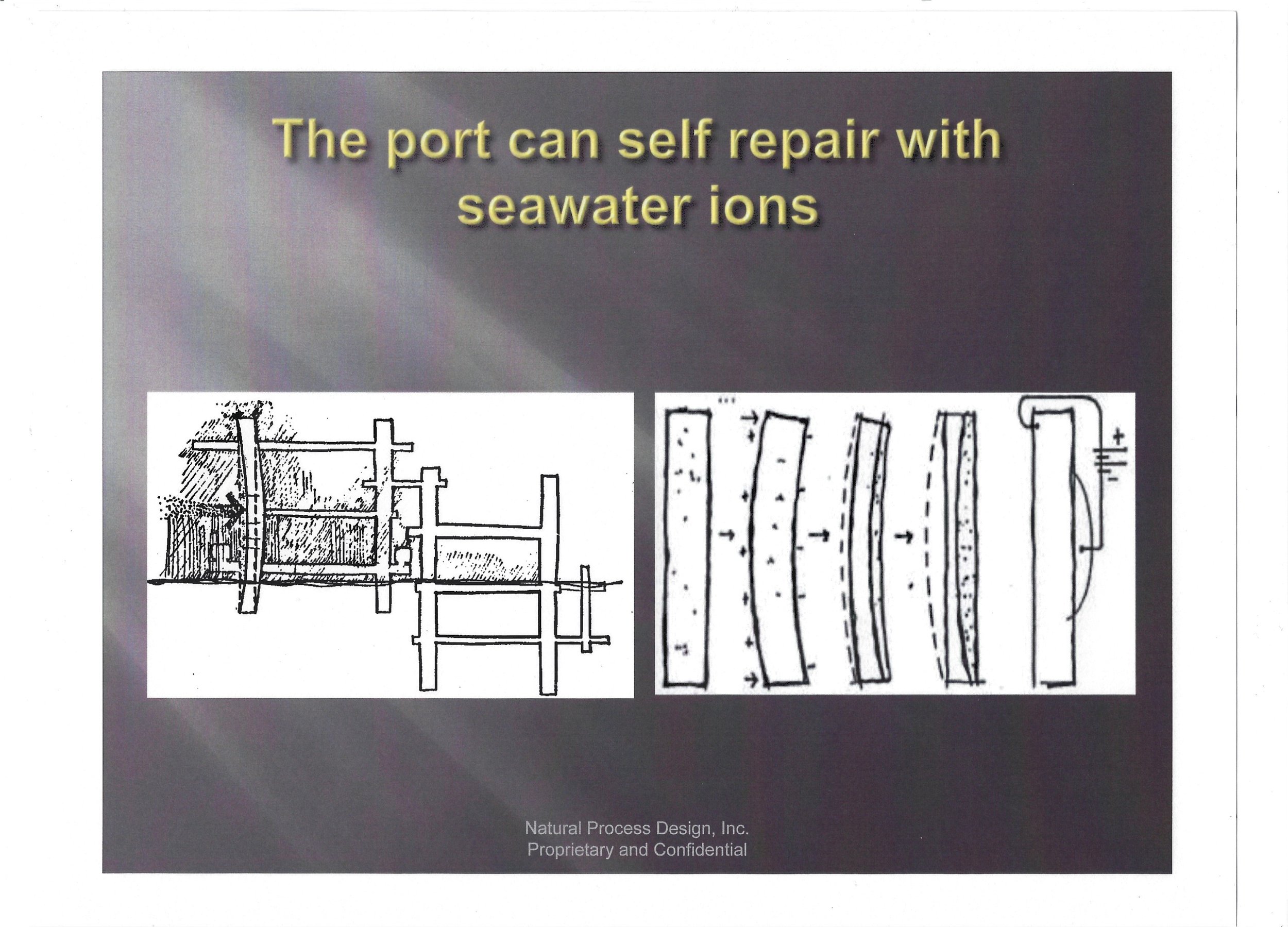
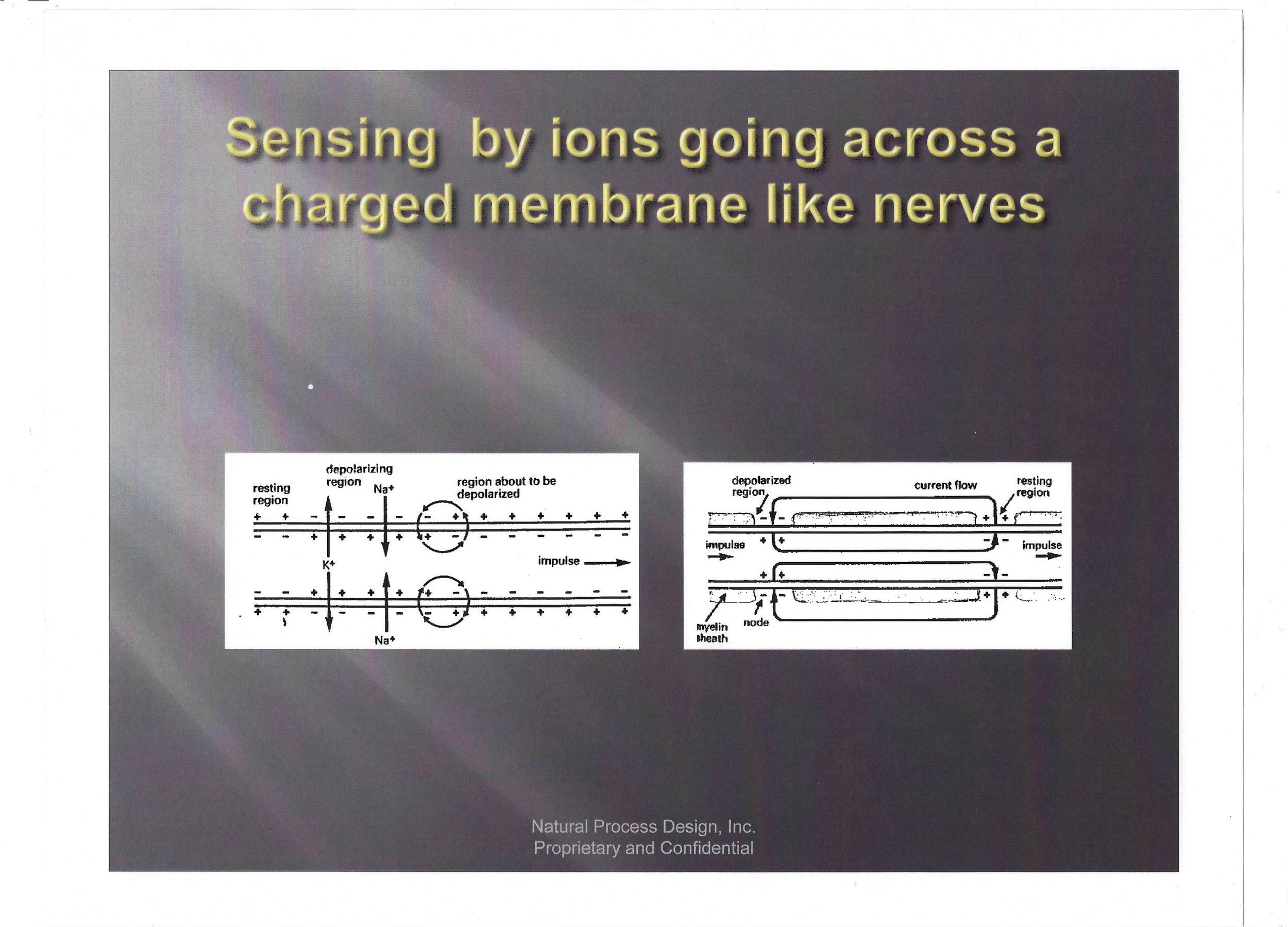
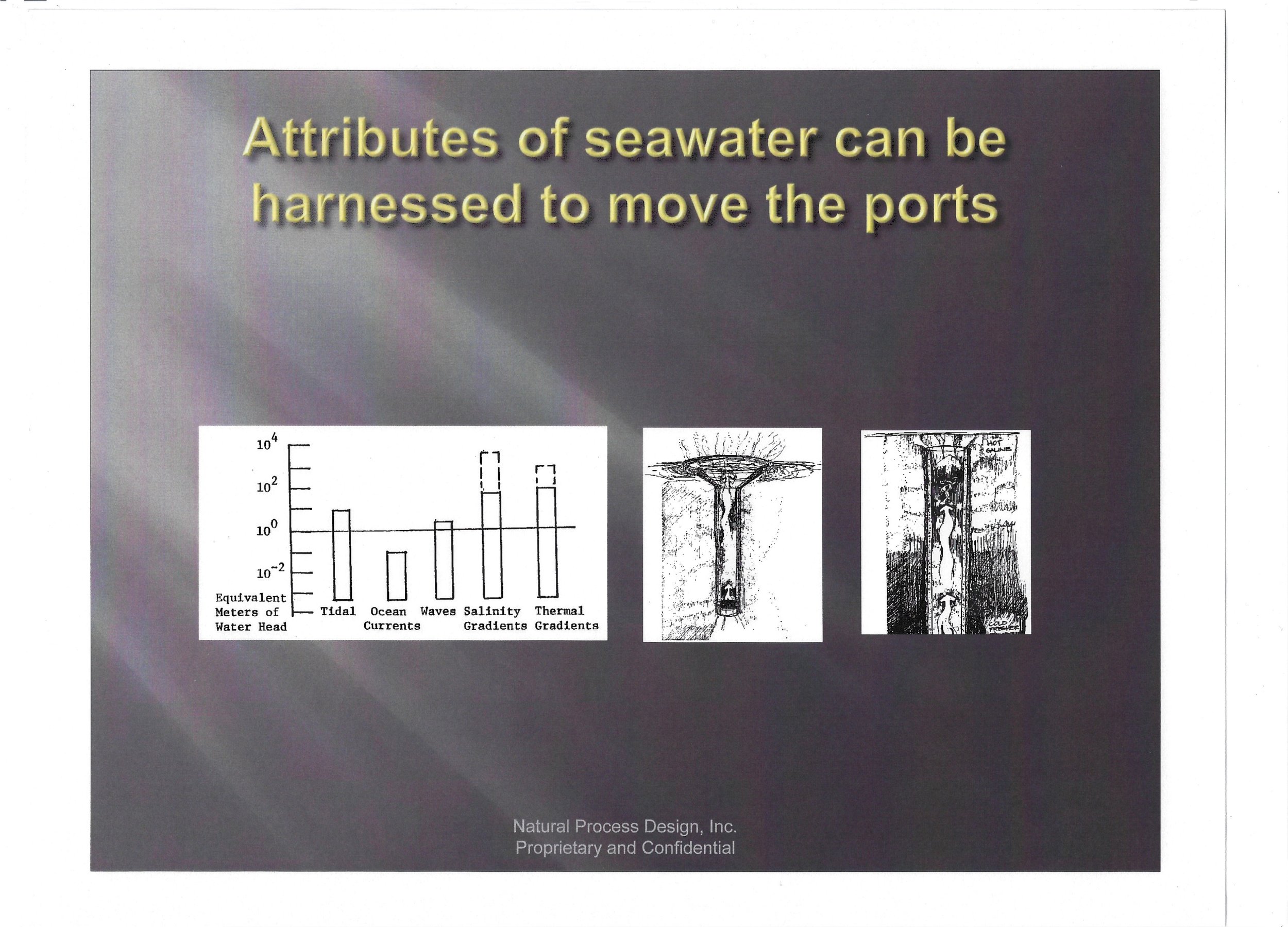
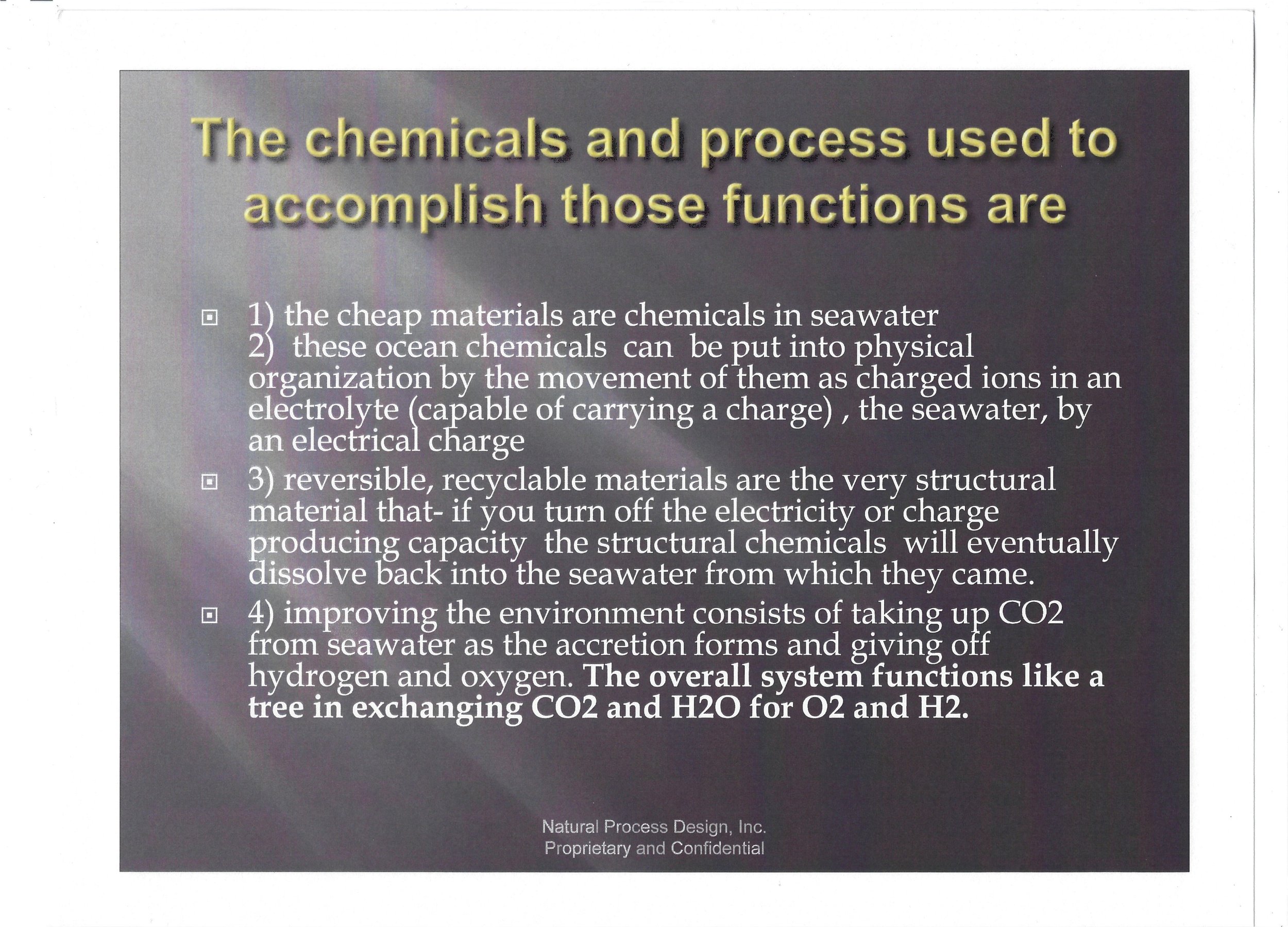
All projects presented in the website are proprietary to Designs by Natural Processes, Inc.